Common Challenges Faced During Industrial Plant Cleaning and How to Overcome Them
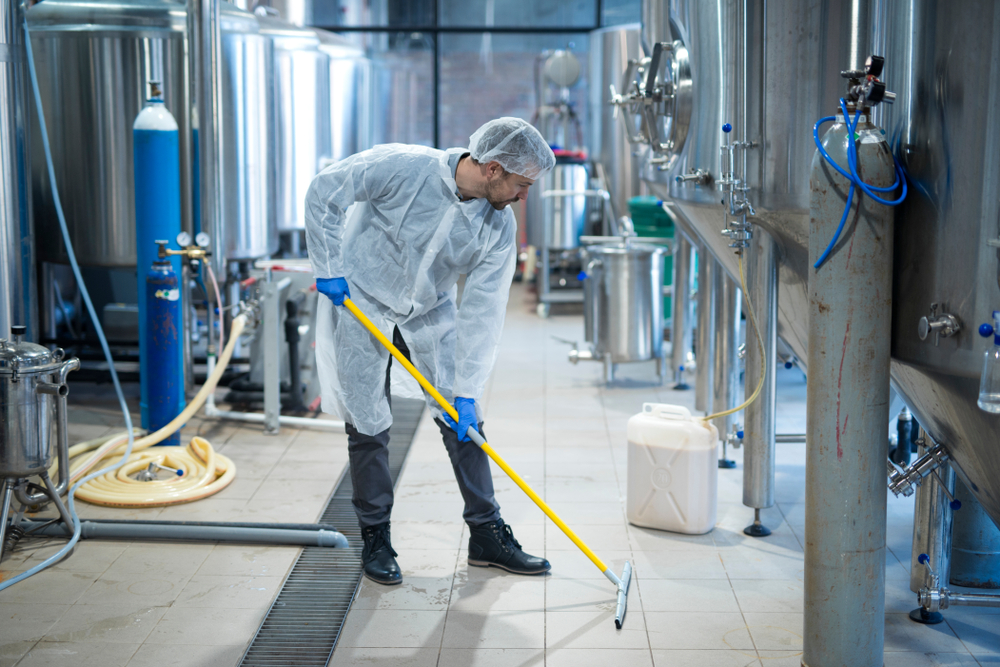
Industrial plant cleaning is a vital yet highly complex task that directly impacts production efficiency, worker safety, and compliance with environmental and health standards. Facilities such as chemical plants, food processing units, refineries, and manufacturing factories all demand rigorous cleaning processes to prevent contamination, reduce downtime, and maintain equipment functionality. However, executing industrial plant cleaning effectively is far from simple. Despite advancements in industrial plant cleaning services, there are still persistent obstacles that facility managers and cleaning crews must tackle. In this comprehensive article, we will explore some of the most common challenges faced during industrial plant cleaning and share effective strategies for overcoming them to ensure a safer, cleaner, and more productive work environment.
The Complexity of Contaminant Types and Surfaces
One of the biggest challenges of industrial plant cleaning is the sheer diversity of contaminants found within a facility. Depending on the industry, these contaminants can include dust, oil, chemical residues, rust, biohazardous materials, and even microbially active growths. Compounding the problem, these pollutants adhere to surfaces made of varying materials such as stainless steel, carbon steel, concrete, plastics, and specialized coatings. Each material responds differently to cleaning agents and mechanical actions, which means a one-size-fits-all approach is destined to fail.
In order to overcome this, industrial plant cleaning services must begin with a thorough assessment of both the contaminants and the surface materials involved. Facilities should maintain a detailed record of their equipment composition and potential pollutant risks. Cleaning teams can then design customized cleaning protocols, carefully choosing detergents, degreasers, and mechanical cleaning methods that match the chemical compatibility of each surface. Using test patches before applying cleaners on a large scale can also help prevent damage while ensuring that contaminants are effectively removed. Staff training on recognizing surface types and the appropriate cleaning procedures is essential to address this challenge holistically.
Ensuring Worker Safety During High-Risk Cleaning
Another common challenge revolves around maintaining worker safety during the industrial plant cleaning process. Facilities often house high-pressure systems, moving parts, hazardous chemicals, and confined spaces that present significant dangers to cleaning personnel. Exposure to fumes, slips and falls, or even chemical burns can be a reality if proper protocols are not followed. Add to this the noise, heat, and physical demands of industrial environments, and the risk multiplies.
To overcome these hazards, industrial plant cleaning services should rigorously enforce Occupational Safety and Health Administration (OSHA) standards and other relevant safety regulations. Employees must be provided with adequate personal protective equipment (PPE) such as gloves, respirators, eye protection, and safety harnesses for working at height. Moreover, before commencing any cleaning operation, a detailed risk assessment should be carried out, identifying potential hazards and documenting control measures. Lockout/tagout procedures should be strictly applied to ensure that machinery cannot accidentally be activated during cleaning. Consistent training, frequent safety audits, and a strong culture of safety awareness across all levels of staff are critical to minimizing the dangers inherent to industrial plant cleaning.
Minimizing Production Downtime
Production downtime is one of the biggest concerns for industrial plants, as every hour of halted operations translates to lost revenue and missed deadlines. Cleaning, while necessary, often requires partial or full shutdowns to ensure both thoroughness and safety. As a result, plant managers may see cleaning as an interruption rather than an investment, leading to shortcuts and deferred maintenance, which ironically increases the risk of future breakdowns or product contamination.
To tackle this challenge, the integration of cleaning with planned maintenance shutdowns is key. Industrial plant cleaning services can coordinate their work with plant engineers to align cleaning tasks with routine inspections, repairs, or equipment replacements. This reduces the need for additional shutdowns and optimizes productivity. Additionally, investing in advanced cleaning technologies such as dry ice blasting, ultrasonic cleaning, or automated cleaning systems can significantly cut down cleaning times while achieving superior results. These technologies often eliminate the need for disassembly and can reach difficult areas without extensive manual labor, providing a faster turnaround. Close communication and collaborative planning between cleaning contractors and plant management will help minimize disruption and maintain operational continuity.
Addressing Environmental Compliance and Waste Management
Industrial facilities must comply with increasingly strict environmental regulations covering wastewater, chemical runoff, air emissions, and the disposal of cleaning residues. Failing to meet these requirements can result in significant fines, reputational damage, and even legal action. The challenge here is that industrial plant cleaning often generates a considerable amount of waste, including hazardous or toxic byproducts that require special handling and disposal.
Overcoming this challenge demands a proactive approach. Facilities should work with industrial plant cleaning services that are well-versed in environmental legislation and waste-handling best practices. Cleaning methods should be chosen with sustainability in mind, favoring biodegradable or environmentally friendly agents whenever possible. Closed-loop cleaning systems that recycle and filter wastewater can greatly reduce the environmental impact. Similarly, proper documentation of waste collection, transport, and disposal helps demonstrate compliance during audits and inspections. Investing in staff training on hazardous waste handling and reporting is another critical measure, ensuring that no step is overlooked in the pursuit of responsible, compliant cleaning practices.
Maintaining Quality and Consistency in Cleaning Standards
One final challenge in industrial plant cleaning is ensuring consistency and quality across multiple cleaning cycles. Unlike household or commercial cleaning, industrial plant cleaning must meet strict standards to protect public health, product quality, and employee safety. However, high staff turnover, inadequate training, and inconsistent supervision can lead to uneven results, exposing the facility to contamination, equipment failures, or even regulatory penalties.
The solution lies in developing clear, repeatable cleaning protocols supported by rigorous quality control processes. Standard operating procedures (SOPs) should be developed for every cleaning task and regularly updated to reflect best practices and changes in the plant’s equipment or production methods. Supervisors should monitor cleaning activities closely, performing routine inspections and documenting any issues for corrective action. Investing in training programs, including refresher courses, helps keep cleaning staff up to date on both procedures and safety standards. Where feasible, the adoption of digital tracking systems and sensors can provide real-time feedback on cleaning performance, offering a data-driven way to maintain high quality and consistency. Partnering with professional industrial plant cleaning services that have a proven track record and robust quality assurance frameworks can further guarantee that cleaning standards are consistently met and maintained.
Conclusion
Industrial plant cleaning is an intricate, high-stakes operation that directly affects safety, production efficiency, and regulatory compliance. The challenges — ranging from diverse contaminants, worker safety risks, production downtime, environmental compliance, and maintaining consistent standards — are formidable but far from insurmountable. With careful planning, investment in modern technologies, thorough staff training, and the expertise of specialized industrial plant cleaning services, these challenges can be effectively addressed. By viewing cleaning as a strategic investment rather than a disruption, industrial facilities can ensure smoother operations, healthier work environments, and greater peace of mind for both their employees and their customers. As industrial demands continue to grow, prioritizing robust, sustainable, and efficient cleaning strategies will remain essential for staying ahead in a highly competitive landscape.
Need Janitorial Services Near You?
There are many ways to clean, but when you want results that “Sparkle,” you call Sparkle Janitorial Services. Traditional cleaning services offer office cleanings limited to vacuuming and trash removal. Our team ensures every surface touched is treated on the regular so that it not only sparkles but also remains hygienic and appealing to your clients. Plus, all of our products and methods are environmentally responsible because we know that the choices we make today will affect the earth we live in tomorrow. Contact us today to learn more about what we can do for you!